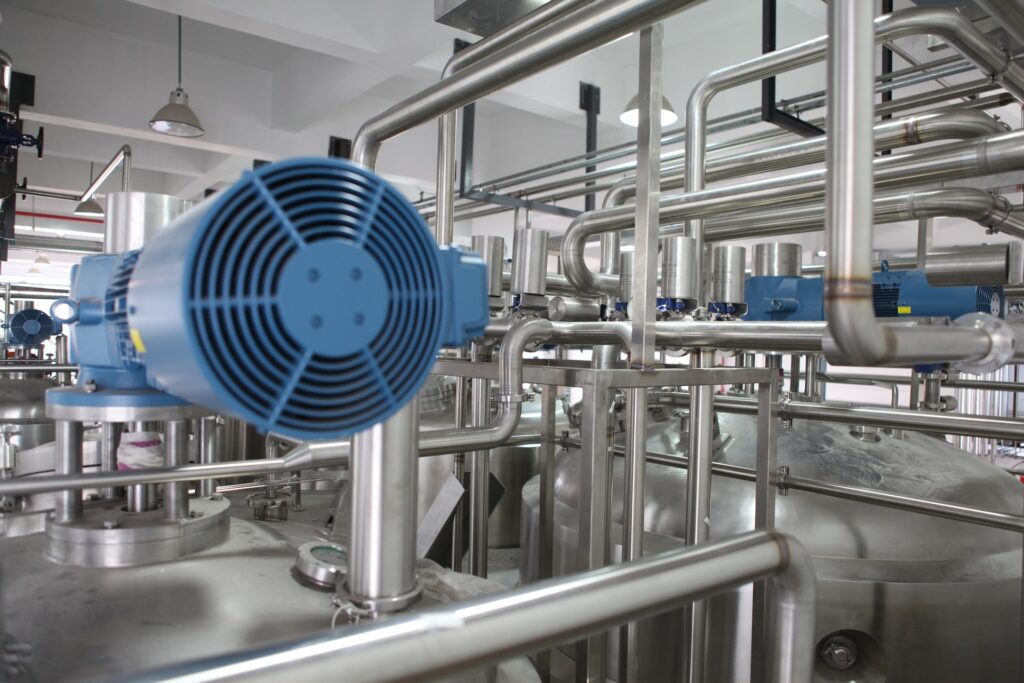
Uses of Rotary Blenders
Rotary blenders have several uses. Among them are mixing, homogenizing, and granulation. These applications depend on the type of material to be mixed. They can be found in many different shapes. They come in vertical, horizontal, and octagonal forms. Each style has its benefits.
octagonal blenders
Octagonal rotary blenders are used for the blending of dry powders, granules, and a variety of other products. These blenders have the advantage of a slow tumbling action, resulting in excellent quality blending. In addition, this type of blending equipment is easy to clean. The octagonal shape of this type of blending machine allows for charging a large amount of material at once. Also, this shape requires fewer RPMs and less space than similar blenders. These blenders can be used for various food, chemical, plastics, and pharmaceutical applications. They are capable of blending dry granules and free-flowing powders. They are especially beneficial for the lubrication of granules.
horizontal blenders
There are many types of horizontal blenders to choose from. Depending on your particular needs, consider a vertical blender, ideal for dry and shear-sensitive materials, or a rotary blender with a rounded shape. The vertical blender is more technologically advanced than the rotary blender. It features a contra-rotating helical ribbon gently moving material up and down through a conical chamber. The resulting mixture can then be discharged through the bottom. The vertical blender also demonstrates some impressive engineering feats, including a gear motor that ensures the high output of the kinematic chain. This allows for a more gentle and efficient blending process. Generally, a rotary blender will have a longer life span than a vertical model. The vertical blender demonstrates some interesting engineering feats, including a winding ribbon and a contra-rotating screw. A gear motor powers the latter to create four cross and gravity flows. Unlike the rotary blender, these processes are less likely to damage the blades. In addition, there are horizontal blenders, which feature safety grids and air pressure valves. These devices are the best for ensuring the safety of your workers and the quality of your products.
Homogenise quality differences in a granulate
A rotary blender is a great way to homogenize granulate quality differences. It can also help reduce the number of bacteria in the mix. This is especially true when dealing with powders such as pharmaceuticals. As mentioned, there is minimal waste in the process. And with the correct blending parameters, operators can achieve consistent blending results. These devices can do everything from lubricating granules to sizing solid dosage powders. Besides, their compact size makes them a practical choice for labs that need more space for a big-ticket machine. The best rotary blenders can handle up to 30 tonnes of output per hour. The rotary mixer is also an excellent choice for thermoplastics processing. It’s the right choice for mixing various liquids, from isopropanol to ethanol.
Process thermoplastics
A rotary blender is used to mix solids and liquids. It is used in various applications, including the pharmaceutical, chemical, and food industries. They are available in a variety of designs, capacities, and finishes. A rotary drum blender is suitable for a variety of applications in the plastics industry. These mixers are equipped with the gentle touch mixing principle, which ensures uniform dispersion of granules. The blenders have internal flights that help promote mixing. These mixers have a wide range of applications, from dusting sticky granulates to mixing fibers, flakes, and mixes. In addition, they can be used as cyclones in a pneumatic conveyor system. A rotary blender is an effective means of mixing a wide range of materials. They come in various capacities, with some able to mix up to 30 tonnes of production output in eight hours.